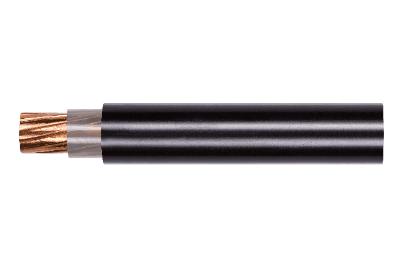
A polietilént (PE) széles körben használjákerősáramú és telekommunikációs kábelek szigetelése és burkolásakiváló mechanikai szilárdságának, szívósságának, hőállóságának, szigetelőképességének és kémiai stabilitásának köszönhetően. A PE szerkezeti jellemzői miatt azonban a környezeti feszültségrepedéssel szembeni ellenállása viszonylag gyenge. Ez a probléma különösen akkor válik szembetűnővé, ha a PE-t nagy keresztmetszetű páncélozott kábelek külső burkolataként használják.
1. A PE burkolat repedésének mechanizmusa
A PE köpeny repedése főként két esetben fordul elő:
a. Környezeti feszültségrepedés: Ez arra a jelenségre utal, amikor a kábelburkolat a kábel telepítése és üzemeltetése után a kombinált feszültség vagy a környezeti közegnek való kitettség miatt rideg repedést mutat a felületről. Ezt elsősorban a burkolaton belüli belső feszültség és a poláris folyadékoknak való hosszan tartó kitettség okozza. Az anyagmódosítással kapcsolatos kiterjedt kutatások lényegében megoldották ezt a repedéstípust.
b. Mechanikai feszültség okozta repedés: Ez a kábel szerkezeti hiányosságai vagy a nem megfelelő köpenyextrudálási folyamatok miatt fordul elő, ami jelentős feszültségkoncentrációhoz és deformáció okozta repedésekhez vezet a kábelfektetés során. Ez a típusú repedés a nagy keresztmetszetű acélszalaggal páncélozott kábelek külső burkolatában hangsúlyosabb.
2. A PE burkolat repedésének okai és javítási intézkedések
2.1 A kábel hatásaAcélszalagSzerkezet
Nagyobb külső átmérőjű kábeleknél a páncélozott réteg jellemzően kétrétegű acélszalag tekercsekből áll. A kábel külső átmérőjétől függően az acélszalag vastagsága változik (0,2 mm, 0,5 mm és 0,8 mm). A vastagabb páncélozott acélszalagok nagyobb merevséggel és rosszabb képlékenységgel rendelkeznek, ami nagyobb távolságot eredményez a felső és az alsó rétegek között. Az extrudálás során ez jelentős különbségeket okoz a páncélozott réteg felületének felső és alsó rétegei közötti köpenyvastagságban. A külső acélszalag szélein lévő vékonyabb köpenyterületek szenvedik el a legnagyobb feszültségkoncentrációt, és ezek azok az elsődleges területek, ahol a jövőben repedések keletkeznek.
A páncélozott acélszalag külső köpenyre gyakorolt hatásának enyhítésére egy bizonyos vastagságú pufferréteget tekerenek vagy extrudálnak az acélszalag és a PE köpeny közé. Ennek a pufferrétegnek egyenletesen sűrűnek kell lennie, gyűrődések és kiemelkedések nélkül. A pufferréteg hozzáadása javítja az acélszalag két rétege közötti simaságot, biztosítja a PE köpeny egyenletes vastagságát, és a PE köpeny összehúzódásával kombinálva csökkenti a belső feszültséget.
A ONEWORD különböző vastagságú anyagokat kínál a felhasználóknak.horganyzott acélszalag páncélozott anyagokhogy kielégítsék a sokféle igényt.
2.2 A kábelgyártási folyamat hatása
A nagy külső átmérőjű páncélozott kábelköpenyek extrudálási folyamatának elsődleges problémái a nem megfelelő hűtés, a nem megfelelő forma-előkészítés és a túlzott nyújtási arány, ami túlzott belső feszültséget eredményez a köpenyen belül. A nagyméretű kábelek vastag és széles köpenyük miatt gyakran korlátozva vannak a vízteknők hosszában és térfogatában az extrudáló gyártósorokon. Az extrudálás során a 200 Celsius-fok feletti hőmérsékletről szobahőmérsékletre történő hűtés kihívást jelent. A nem megfelelő hűtés lágyabb köpenyt eredményez a páncélréteg közelében, ami karcolásokat okozhat a köpeny felületén, amikor a kábelt tekercselik, ami végül repedésekhez és törésekhez vezethet a kábelfektetés során külső erők hatására. Ezenkívül a nem megfelelő hűtés hozzájárul a belső zsugorodási erők növekedéséhez a tekercselés után, növelve a köpeny repedésének kockázatát jelentős külső erők hatására. A megfelelő hűtés biztosítása érdekében ajánlott a vízteknők hosszának vagy térfogatának növelése. Elengedhetetlen az extrudálási sebesség csökkentése, miközben fenntartják a megfelelő köpeny lágyulását és elegendő időt biztosítanak a hűtésre a tekercselés során. Továbbá, mivel a polietilént kristályos polimerként tekintjük, a szegmentált hőmérsékletcsökkentéses hűtési módszer, 70-75°C-ról 50-55°C-ra, végül szobahőmérsékletre, segít enyhíteni a belső feszültségeket a hűtési folyamat során.
2.3 A tekercselési sugár hatása a kábel tekercselésére
A kábeltekercselés során a gyártók az ipari szabványokat követik a megfelelő szállítódobok kiválasztásánál. A nagy külső átmérőjű kábelek hosszú szállítási hosszainak biztosítása azonban kihívást jelent a megfelelő dobok kiválasztásában. Az előírt szállítási hosszúságok betartása érdekében egyes gyártók csökkentik a dobhenger átmérőjét, ami a kábel hajlítási sugarainak elégtelenségét eredményezi. A túlzott hajlítás a páncélrétegek elmozdulásához vezet, ami jelentős nyíróerőket okoz a burkolaton. Súlyos esetekben a páncélozott acélszalag sorjái átszúrhatják a párnázó réteget, közvetlenül beágyazódnak a burkolatba, és repedéseket vagy hasadékokat okozhatnak az acélszalag szélén. A kábelfektetés során az oldalirányú hajlító és húzóerők a burkolat repedését okozzák ezeken a repedéseken, különösen a dob belső rétegeihez közelebb lévő kábelek esetében, ami hajlamosabbá teszi őket a törésre.
2.4 A helyszíni építési és telepítési környezet hatása
A kábelépítés szabványosítása érdekében ajánlott minimalizálni a kábelfektetés sebességét, elkerülve a túlzott oldalirányú nyomást, hajlítást, húzóerőket és felületi ütközéseket, biztosítva a civilizált építési környezetet. A kábelfektetés előtt lehetőleg hagyjuk a kábelt 50-60°C-on pihenni, hogy a köpeny belső feszültsége felszabaduljon. Kerüljük a kábelek hosszan tartó közvetlen napfénynek való kitételét, mivel a kábel különböző oldalain a hőmérséklet-különbség feszültségkoncentrációhoz vezethet, növelve a köpeny repedésének kockázatát a kábelfektetés során.
Közzététel ideje: 2023. dec. 18.